Supplier Audits: Ensuring Quality and Reducing Risks
- Aniekpeno Ifeh
- Feb 12
- 4 min read
Updated: Feb 13
When working with suppliers, you want to be sure they deliver high-quality products and follow the right standards. One of the best ways to achieve this is through supplier audits. Whether you're evaluating a new supplier or maintaining a long-term partnership, these audits provide valuable insights into their operations and compliance. A strong supplier audit program can lead to better supplier relationships, improved accountability, and stronger supply chain resilience.
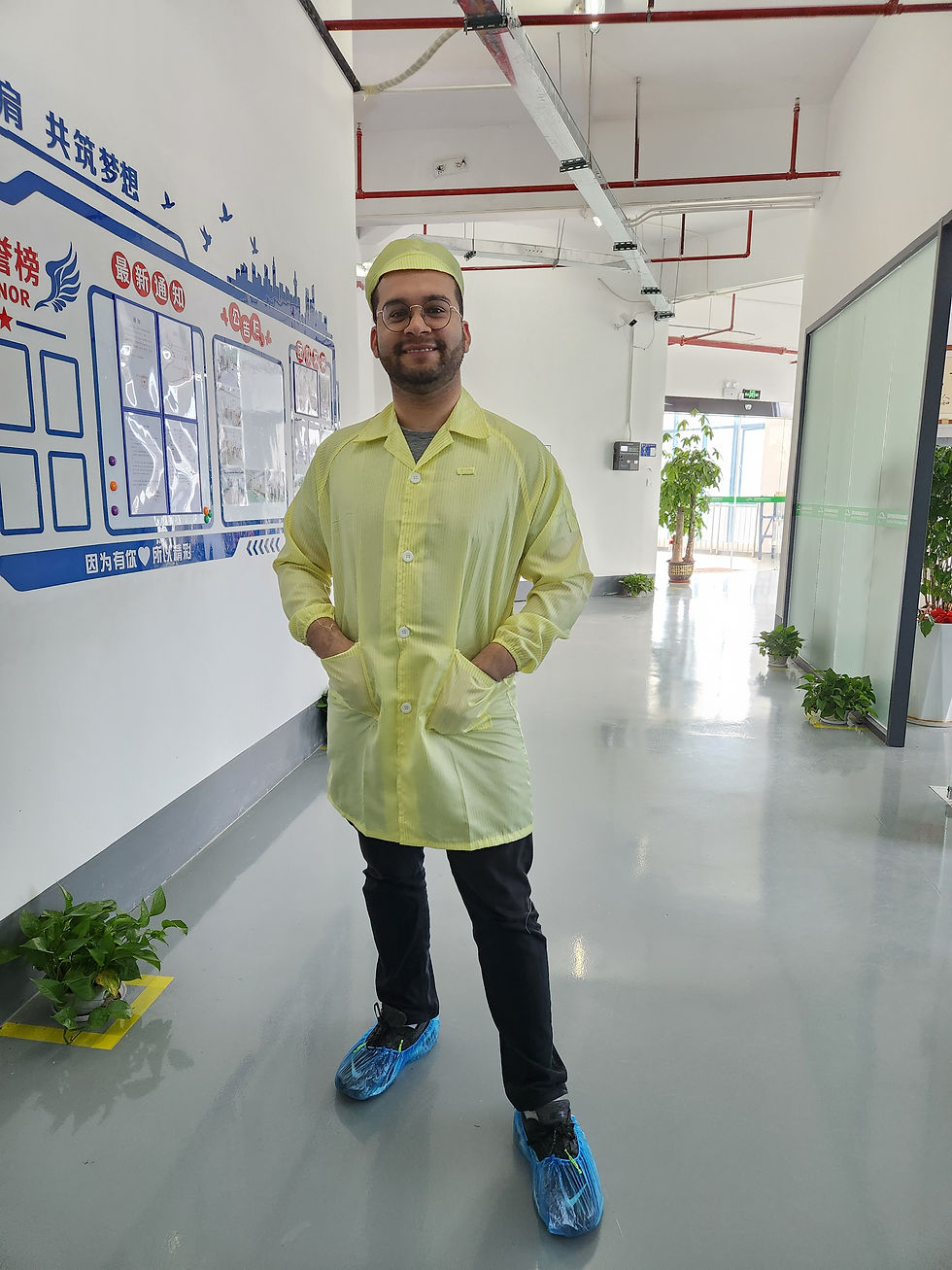
Why Are Supplier Audits Important?
Supplier audits help prevent potential problems before they arise. They provide a structured approach to evaluating supplier performance and ensuring long-term business success.
Here’s why they matter:
Minimizing Risks – Audits identify potential issues before they affect production, helping businesses mitigate risks and avoid disruptions.
Ensuring Quality – Regular checks confirm that suppliers maintain consistent product standards, preventing defects and ensuring customer satisfaction.
Regulatory Compliance – Audits verify that suppliers follow industry regulations, reducing the risk of fines, legal issues, or non-compliance penalties.
Optimizing Processes – Evaluating supplier operations can reveal areas for improvement, making processes more efficient and cost-effective.
Cost Savings – Detecting problems early prevents expensive production delays, product recalls, and reputational damage.
Strengthening Supplier Relationships – A transparent audit process fosters open communication and trust between businesses and their suppliers.
Enhancing Brand Reputation – Ensuring ethical and sustainable supplier practices helps businesses maintain a positive public image and meet consumer expectations.
Types of Supplier Audits
Different audits serve different purposes:
New Supplier Evaluation – Conducted before forming a partnership, this audit ensures the supplier has the necessary skills, tools, and reliability to meet expectations.
Process Audit – Focuses on production processes to ensure efficiency, consistency, and quality control while identifying areas for optimization.
Quality Audit – Verifies that a supplier’s quality management system meets international standards such as ISO 9001, ensuring consistent quality.
Social Compliance Audit – Examines workplace conditions to ensure fair labour practices, worker safety, and ethical treatment of employees.
Environmental Audit – Assesses whether the supplier follows sustainability and environmental regulations, such as reducing carbon footprint and waste management.
Security Audit – Evaluates data protection and supply chain security to prevent breaches, cyber threats, and unauthorized access to sensitive information.
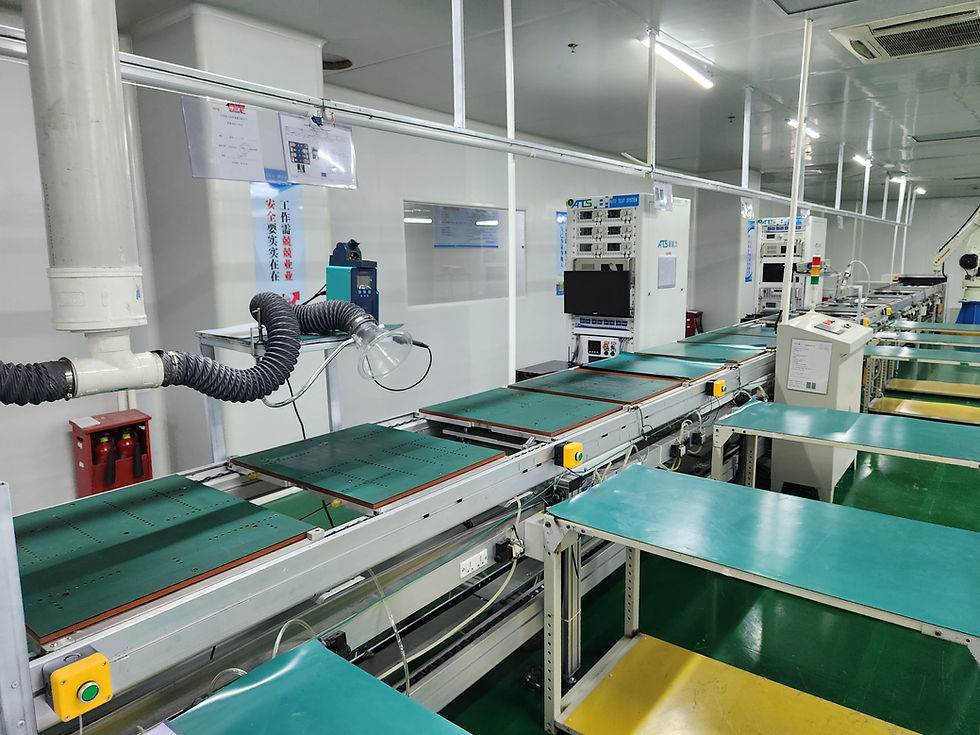
How to Conduct an Effective Supplier Audit
A successful audit follows these steps:
Define Objectives – Identify key focus areas such as product quality, regulatory compliance, or operational efficiency to align the audit with business goals.
Develop an Audit Checklist – Outline essential criteria based on industry standards, company requirements, and best practices to ensure consistency.
Conduct the Audit – Perform an on-site or remote audit using structured evaluation methods, interviews, and documentation reviews.
Analyze Findings – Review the results to determine strengths, weaknesses, and areas for improvement, using data-driven insights.
Implement Corrective Actions – Work with the supplier to address identified issues, develop action plans, and track progress over time.
Monitor and Reassess – Schedule follow-up audits to ensure ongoing compliance, continuous improvement, and a proactive approach to risk management.
Document Everything – Maintain detailed records of audit findings, corrective actions, and follow-up measures to track progress and inform future audits.
Red Flags to Watch For
During an audit, be alert for these warning signs:
Inconsistent Record-Keeping – Poor documentation or missing records may indicate unreliable quality control and lack of transparency.
Lack of Transparency – A supplier reluctant to share key information or avoid specific questions could be hiding compliance issues or unethical practices.
Frequent Product Defects – High defect rates suggest weak quality management practices, poor manufacturing processes, or inadequate employee training.
Unethical Working Conditions – Labor violations, unsafe environments, or worker mistreatment can lead to reputational damage and legal consequences.
Failure to Meet Deadlines – Constant delays in production or delivery may indicate inefficiencies, lack of capacity, or management issues.
Ignoring Corrective Actions – If a supplier fails to implement suggested improvements from previous audits, it raises concerns about long-term reliability and accountability.
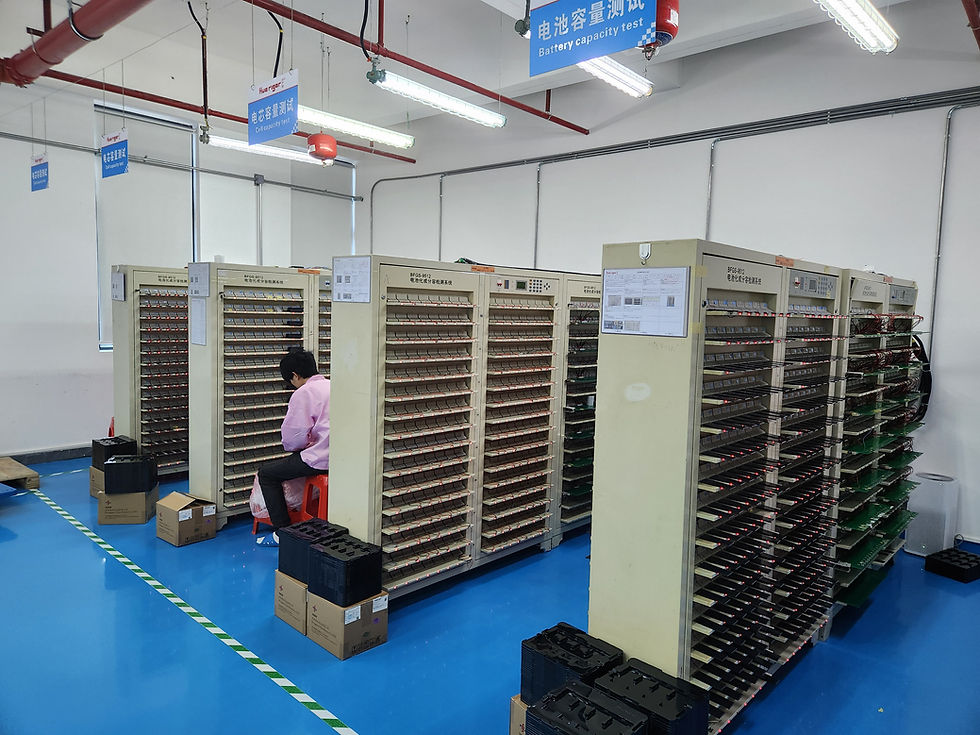
Best Practices for Maintaining a Strong Supplier Audit Program
To maximize the benefits of supplier audits, companies should:
Schedule Audits Regularly – Implement a routine audit schedule to monitor supplier performance and prevent issues from escalating.
Use a Risk-Based Approach – Prioritize high-risk suppliers for more frequent and in-depth audits.
Leverage Technology – Utilize digital tools and audit management software to streamline the audit process, track compliance, and analyze data efficiently.
Foster Open Communication – Encourage suppliers to view audits as collaborative efforts rather than punitive measures, promoting transparency and continuous improvement.
Train Internal Teams – Equip procurement and quality teams with the skills needed to conduct thorough and effective supplier audits.
Set Clear Expectations – Establish audit criteria and expectations upfront, so suppliers understand the standards they need to meet.
Follow Up on Action Plans – Ensure that corrective actions are being implemented and assess their impact through follow-up evaluations.
Final Thoughts
Supplier audits are essential for maintaining quality, ensuring compliance, and minimizing risks. Whether you're assessing a new supplier or monitoring an existing one, regular audits help keep operations smooth and reliable. A well-structured audit program can lead to stronger partnerships, better accountability, and a more resilient supply chain.
By following best practices and continuously improving the audit process, businesses can safeguard their reputation, enhance product quality, and reduce risks. Supplier audits are not just about compliance, they are a strategic tool for long-term success.
Have you conducted a supplier audit before? What was your experience? Share your thoughts in the comments!
Comments