How Experience Improves Manufacturing Efficiency and Reduces Costs
- Mohammed Abid Ali
- Feb 20
- 4 min read
For companies focused on manufacturing, efficiency and cost reduction are key priorities. The experience effect refers to how accumulated knowledge and continuous improvements in production processes lead to greater efficiency and lower costs. The more a company manufactures, the more it learns, allowing for smarter decision-making, streamlined operations, and increased profitability. Understanding and applying this effect is essential for businesses looking to maintain a competitive edge.
By leveraging past experiences, manufacturers can significantly cut costs, enhance productivity, and improve product quality. As new technologies emerge and manufacturing techniques evolve, companies that actively integrate learning into their operations can stay ahead of competitors and achieve long-term sustainability.
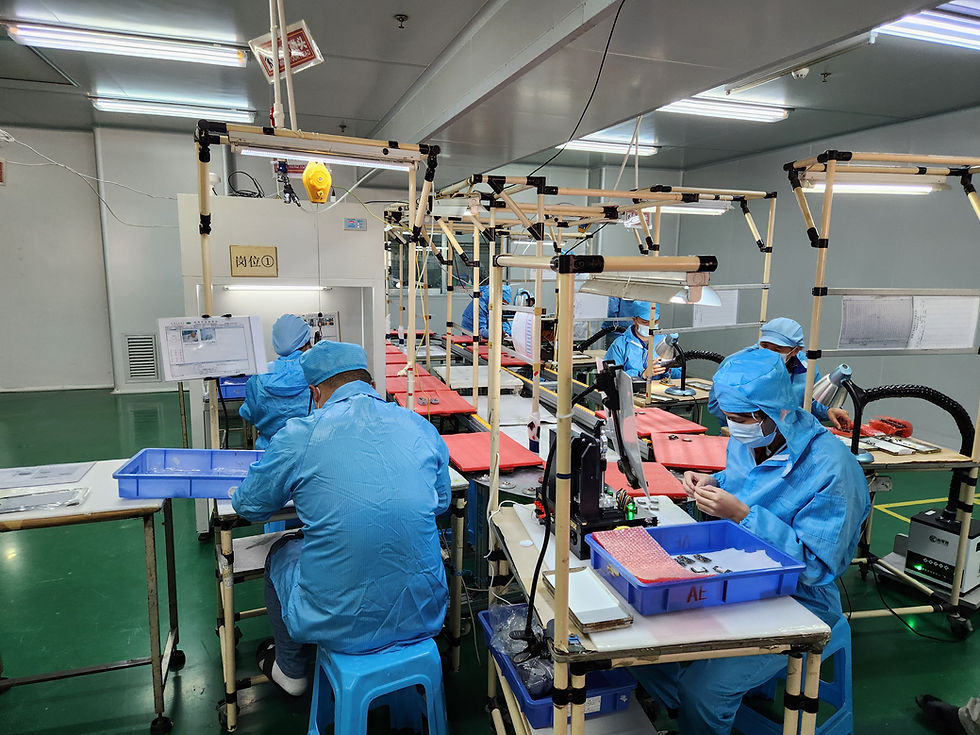
Understanding the Experience Effect in Manufacturing
The experience effect, or the learning curve effect, explains why production costs decrease as teams refine their workflows, equipment, and technology over time. In manufacturing, this principle is crucial for improving processes, reducing waste, and increasing output quality. It also allows businesses to develop expertise in their specific production methods, leading to better resource management and innovation in manufacturing strategies.
Key Benefits of the Experience Effect
Process Optimization – Manufacturers refine their production steps to minimize inefficiencies and reduce cycle times.
Workforce Learning – As employees gain experience, they improve in precision and productivity, reducing errors and rework.
Technology Enhancements – Ongoing improvements in automation and machine learning enhance manufacturing efficiency.
Material and Resource Management – Optimizing supply chains and reducing waste lowers overall production costs.
Quality Control Improvements – Experience leads to better quality assurance measures, reducing defects and product recalls.
Scalability – As companies grow, they implement best practices that improve efficiency at larger production scales.
Customization Capabilities – Experienced manufacturers can efficiently adapt processes to meet customized production demands.
Risk Mitigation – Companies that consistently improve their processes through experience can better anticipate and mitigate operational risks.
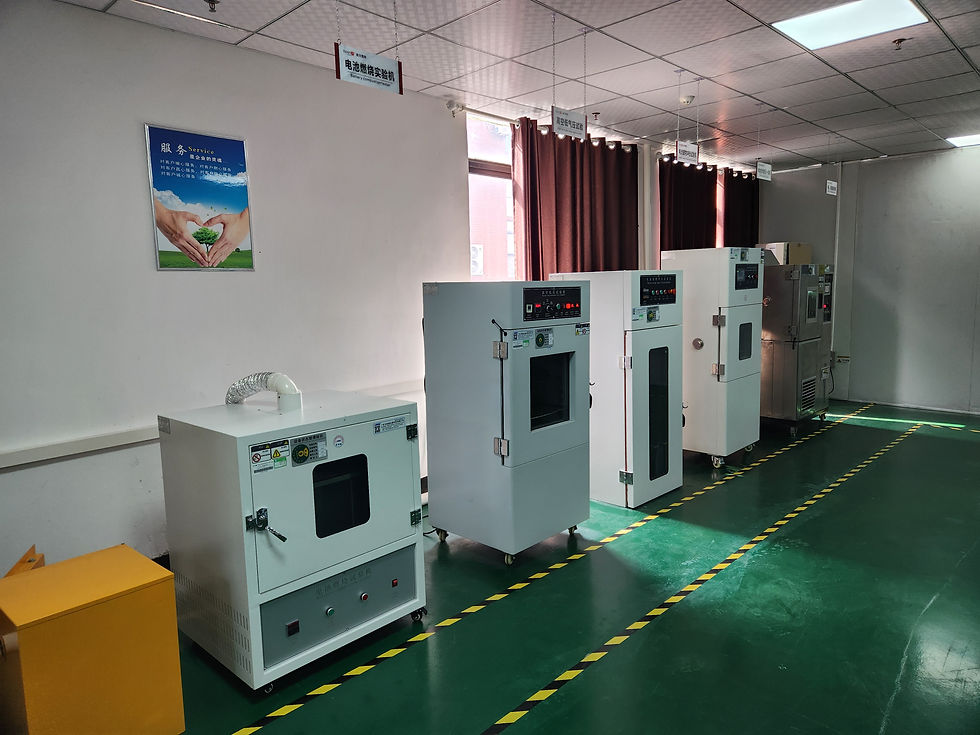
How the Experience Effect Reduces Costs
The experience effect drives cost reductions in multiple ways:
Higher Labor Productivity
Employees become more skilled with repetition, leading to faster production times and fewer errors. Training programs and well-documented procedures further enhance efficiency. Over time, companies can reduce training costs as employees become more proficient in their roles.
Refined Production Workflows
Companies refine their processes over time, eliminating unnecessary steps and integrating automation for faster and more precise manufacturing. Continuous process evaluation and improvement help businesses keep up with industry standards and ensure optimal performance.
Investment in Smart Technology
Upgraded machinery, AI-driven production monitoring, and robotics improve accuracy and reduce human error, lowering production costs. Data analytics and real-time monitoring also help manufacturers track inefficiencies and proactively address potential bottlenecks.
Supply Chain Optimization
Stronger supplier relationships and improved forecasting allow manufacturers to negotiate better prices and reduce material waste. A well-optimized supply chain minimizes disruptions, lowers transportation costs, and enhances overall production reliability.
Defect Reduction and Product Quality
Experience leads to better quality control processes, reducing scrap rates and ensuring fewer defects reach the customer. Improved quality management results in higher customer satisfaction, fewer returns, and enhanced brand reputation.
Energy and Resource Efficiency
More experienced manufacturers find ways to optimize energy use, reduce material waste, and adopt sustainable production methods. Incorporating green manufacturing practices not only reduces costs but also aligns with environmental regulations and corporate social responsibility goals.
Faster Adaptation to Market Changes
Companies that have accumulated experience in mass production can pivot more efficiently when faced with changing market demands. They can introduce new products faster, adjust pricing strategies, and respond effectively to shifts in consumer preferences. Experience also enables manufacturers to anticipate industry trends and make data-driven investment decisions.
Improved Equipment Maintenance and Longevity
With experience, manufacturers develop effective maintenance schedules that extend the lifespan of equipment, reducing downtime and costly repairs. Predictive maintenance strategies ensure that machinery operates at peak performance, minimizing unexpected breakdowns.
Industries Where the Experience Effect is Most Impactful
For companies engaged in manufacturing, the experience effect plays a significant role in:
Electronics and IoT Devices – Refining assembly processes for precision and efficiency.
Industrial Equipment Manufacturing – Improving production workflows and material handling.
Automotive and Aerospace – Enhancing automated systems and quality control standards.
Sustainable Manufacturing – Reducing environmental impact while increasing cost savings.
Medical Device Production – Ensuring high-precision manufacturing with continuous process improvements.
Food and Beverage Processing – Enhancing consistency and safety in mass production environments.

Strategies for Leveraging the Experience Effect in Manufacturing
To maximize the benefits of the experience effect, manufacturers should focus on:
Ongoing Workforce Training – Ensuring employees stay up to date with new technologies and best practices.
Data-Driven Process Improvements – Using performance metrics to identify areas for refinement and implementing strategic improvements.
Automating Repetitive Tasks – Implementing robotics and AI to reduce manual labour and improve accuracy.
Investing in Predictive Maintenance – Reducing downtime by anticipating equipment failures before they occur.
Sustainable Practices – Reducing waste, energy use, and material costs through optimized production methods.
Supply Chain Efficiency – Working closely with suppliers to reduce lead times, source cost-effective materials, and minimize disruptions.
Standardizing Processes – Ensuring consistent production methods to improve quality and reduce variability.
Encouraging Cross-Team Collaboration – Sharing knowledge across departments to foster innovation and efficiency.
Testing and Prototyping – Using experience-driven insights to refine product designs before full-scale production.
Customer Feedback Integration – Learning from customer feedback to improve product features and performance over time.
Final Thoughts
For manufacturers, the experience effect is a crucial tool for improving efficiency, reducing costs, and maintaining high-quality production. By continuously refining processes, investing in automation, and training employees, companies can enhance their competitiveness and long-term success.
Businesses that prioritize continuous learning and innovation will be best positioned to adapt to industry changes and drive sustainable growth. The ability to learn from past experiences, apply data-driven insights, and integrate new technologies ensures that manufacturers remain agile in a rapidly evolving marketplace.
If you want to see how experience can help your manufacturing business? Get in touch with us today to learn how our custom solutions can help you save money and work more efficiently.
Comments